Ultrasonic welding is a pressure and friction welding technique
The oscillator system consists of three components: converter, booster and sonotrode. The converter transforms the high-frequency voltage into mechanical oscillation via piezo elements.
The booster is similar to an amplifier. The mechanical oscillation from the converter can either be amplified or reduced using a booster so that the amplitude of the sonotrode is optimized for its later use.
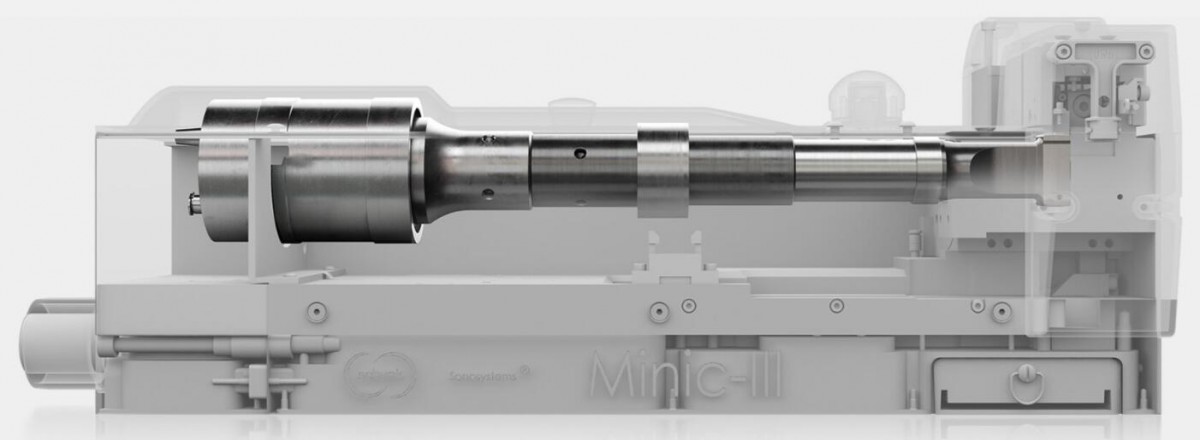
The sonotrode is the essential element; it transfers the high-frequency oscillation to the component being welded. For transferring the oscillation the sonotrode has a profile at the point of contact with the surface of the component which can be designed to be coarse or fine, depending on the welding task at hand.
Depending on the application, the oscillator systems are set to different frequencies. The most usual frequencies are 20 kHz 35 and 40 kHz. The rule here is that with increasing frequency the size of the oscillator system and the maximum transferrable welding power for joining components decreases.
Substance-to-substance bonding through metal welding
While in the case of plastic welding the parts being joined are brought into a liquid state, the bond is generated with both parts in a solid state during the metal-welding process. Although the melting point of the metals being bonded is never reached, high-strength metal bonds can be realized which are very similar to those achieved with conventional friction-welding processes. Ultrasonic metal welding results in a solid, homogenous and permanent metal bond far superior to surface adhesion or gluing. The two metallic materials permeate each other and are permanently and metallically bonded through short-distance diffusion within a fraction of a second.